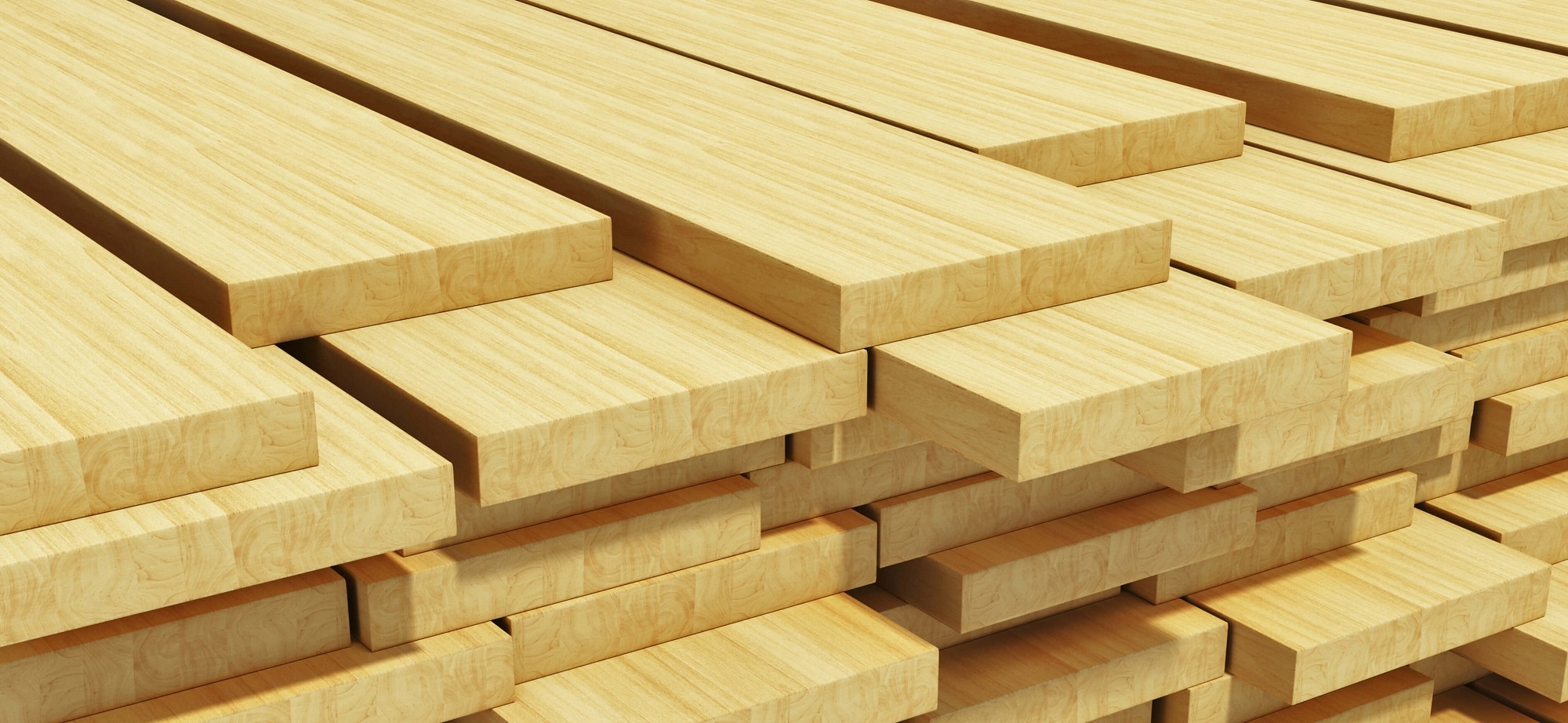
- Главная
- Категории
- Деревообработка
- Windows CNC Technology
- Conturex 226
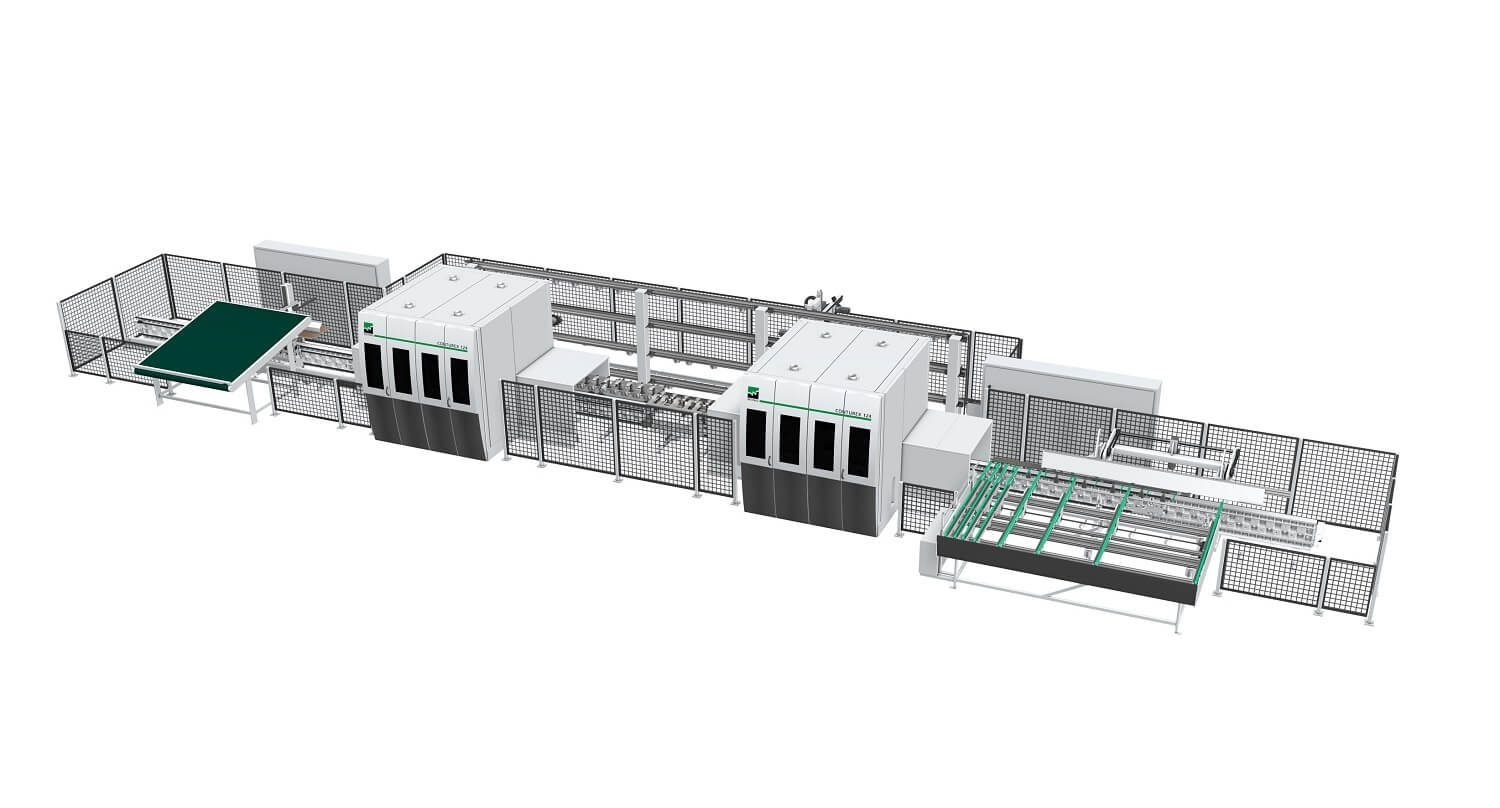
WEINIG
Conturex 226
Greater flexibility in woodworking
No compromises – in industrial window production, you need optimal performance and flexibility.
The Conturex 226 achieves the maximum expansion level in the one-man machine segment. Solutions are available in the system area for further performance enhancement.
Four tables and four main spindles share the processing stages to create a seamless and highly efficient process. This enables three parts to be processed simultaneously.
The variety of products and systems in windows, doors and facades is steadily increasing. Processing of individual pieces is correspondingly complex. Not only are transverse and longitudinal processing and drilling required in high quality, elaborate processing such as rabbet joint milling, lock housing and dovetail joints are also required for facade and conservatory parts.
Preparations for fittings are also of the utmost importance. This includes all drillings and milling for door handles, corner/scissor bearings, drilling plugs or notched holes for locking elements, door hinges of various designs, multi-point locks, drillings for cable feedthroughs and installation, handle shells on lift-slide doors and much more besides. The Conturex meets even these requirements highly flexibly and fully automatically.
iTronic operating components
1. Adaptive trimming blade
Full adaptive trimming blades with automatic pressure adaptation to match edge thickness and height. Your advantages:
Always the right pressure for different types of edging
Prevents unnecessary vibration
Reduces wear
2. Automatic pressure unit
The contact pressure of the individual pressure rollers is adapted perfectly to the application by an intelligent pneumatic system. Your advantages:
Reduces reject quotas to a minimum
Eliminate sample workpieces
Optimum machining results even for continuously changing applications
3. Automatic glue quantity control
Automatic, requirement-adapted control of glue quantity with program selection: Always optimum glue application for:
Various types of panels, e.g. chipboard or MDF
Various panel thicknesses
Various feed rates
EVA or PUR glue
Adaptation to processing parameters for glue from different manufacturers
4. Automatic cleaning routine
Integrated, fully-automatic purging routine for PUR glue at the touch of a button on the control. This process completely purges the machine, full automatically, with the correct quantity of cleaner, at the right temperature and contact pressure. (Cleaning is required after 48 h = PUR reaction time). Your advantages:
Best system on the market
PUR glue always under control
Avoids errors during cleaning operation
5. Remaining glue quantity indicator
The remaining quantity of glue as well as the running meters that can still be processed are automatically monitored by a special sensor in the system and displayed to the operator on the control. Your advantages:
Operator knows how many running meters can still be produced at all times
Professional supervision of the cleaning process
Optimization of remaining quantity of glue in system at time of cleaning process.